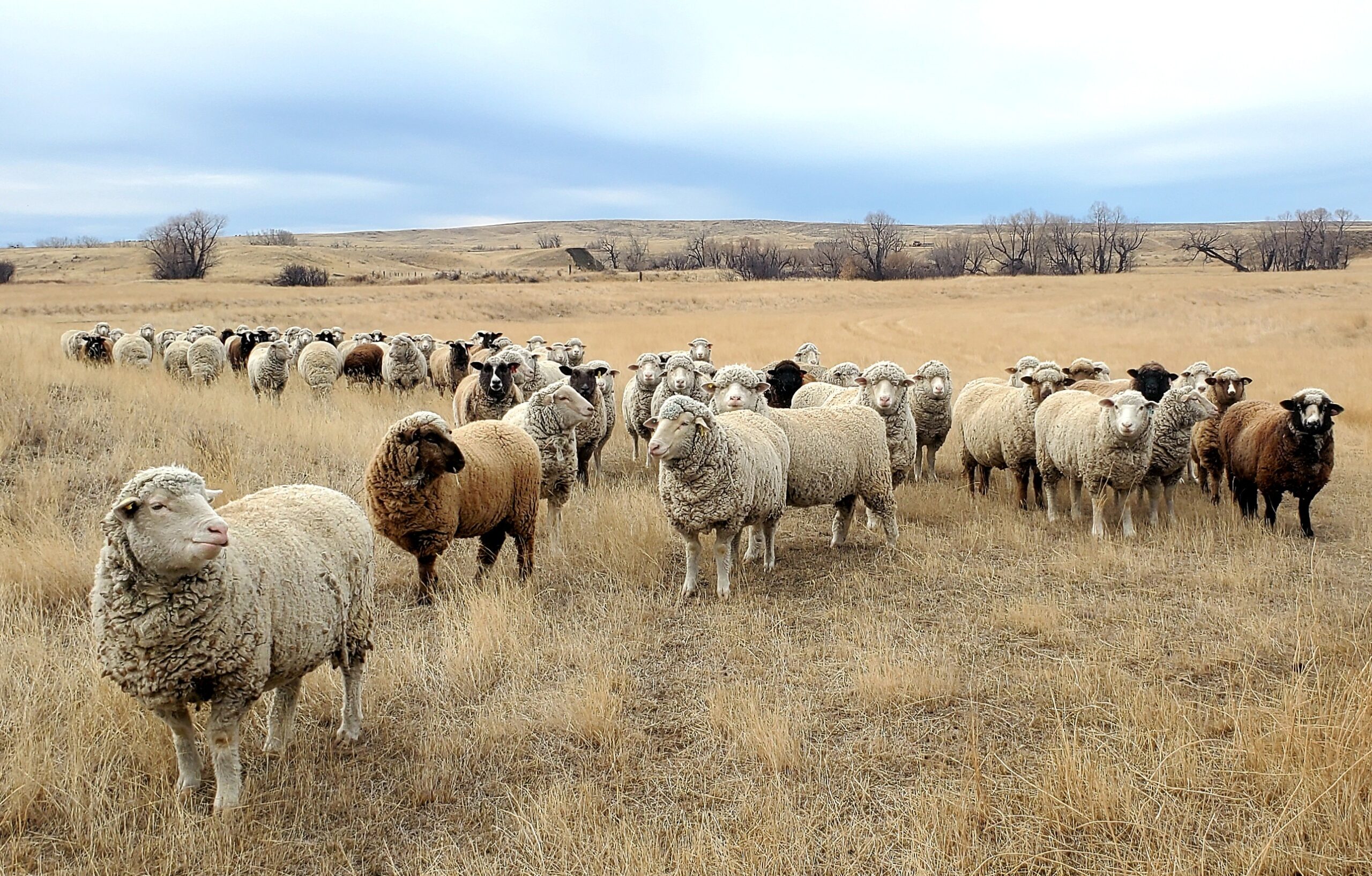
Wool is finally getting love in NYTimes Art & Design, but the story is a little fuzzy on facts
I was thrilled to read the recent New York Times Art & Design article, 11,000 Years of Designer Sheep. It’s about time American wool was in the spotlight! But some of the statements in the article were a little too fuzzy for me – a longtime ovine evangelist and fiber fanatic – to let stand without comment.
The article covered the “Formafantasma – Oltre Terra” exhibit that opened on February 15 at Stedelijk Museum in Amsterdam. The exhibit explores the “paradox of mutual reliance” between humankind and sheep and how this symbiotic relationship has developed. And I agree this is a rich story. It deserves to be told accurately.
Quotes pulled from Nina Siegal’s New York Times article have substance but they obscure important truths about the versatility of sheep and wool, and the creative ways both can contribute to humanity. In various places the article states that “Over hundreds and hundreds of years, tame sheep have developed through human design so that it would become a wool-producing machine with ears and eyes, instead of an animal. . . . For centuries, we have relied on sheep’s wool for clothing and blankets and they relied on us for shearing. Now, sheep can’t molt with human help, though we’re using little of their wool. . . . (R)eliance on human intervention {i.e., shearing} reflects one small way in which we have, over centuries, “designed” sheep rather poorly.”
Well, not exactly.
Humans and sheep have co-evolved for more than 10,000 years and we’ve created over 1,400 recognized breeds and countless crossbreeds in that time. Some breeds have hair that molts (aka sheds, falling out of its own accord) like ancestral sheep and today’s Rocky Mountain bighorns, while other breeds retain their fiber until it’s sheared. It’s worth noting that hair is a very different fiber than wool: a hair shirt will be incredibly itchy, heavy and not very warm compared to a whisper soft, light, warm shirt knit from merino wool. That’s why hair shirts are for penance or enemies while merino shirts are for pampering oneself and loved ones!
Over centuries shepherds have crafted sheep to fit every need and place, including many that grow fine, soft wool. Those sheep – usually with some degree of merino heritage – do require shearing. But in contrast to the NYT article, there are also wool sheep that shed their fleeces without shearing. Shetland, Icelandic and other “primitive” sheep shed their wool annually. These small, hardy sheep were sprinkled on islands throughout the north Atlantic by 8th century Vikings, then often left on their own to adapt or die. These breeds “roo” in spring, when shifting hormones cause a break in their wool just in time to trigger the shedding of their heavy winter coat for lighter summer wear.
Rooing breeds have a layer of long, coarse, water-resistant wool known as “tog” that shields a short, fine and fabulously soft inner layer of wool called the “thel.” While rooing can happen without human intervention, shepherds often pluck these patches of molting wool, then put it to good use: those early Vikings crossed oceans with sails woven from the rooed wool of sheep. I’m writing this article while wearing a sweater knit from the rooed thel of Shetland sheep.
So do we need to “redesign” sheep to produce wool without shearing, as the Ormafantasma – Oltre Terra exhibit explores? Heck no! Woolgrowers have good reason for wanting sheep not to shed. It’s all about producing fine, consistent, high-quality fiber that can be grown, harvested (yes, through shearing) and processed efficiently at scale to meet global textile demand. Quick facts:
- Hair sheep shed but their fiber isn’t suited to textile manufacture. It’s too short, straight and coarse.
- Wool that naturally sheds (from sheep that roo) is difficult to harvest efficiently. Because rooing is a type of molting, it proceeds over time from one end of the sheep to the other and results in some wool still holding tight to the skin while other breaks off and blows away. Personal experience is that it’s no fun to pluck your wool crop one handful at a time from thorny bushes or chase it down in gusty winds.
- Rooing sheep are double-coated. While there are a lot of good uses for both thel and tog, for standard clothing manufacture you have to physically separate the two. Commercial woolgrowers have intentionally bred sheep not only to be single-coated, but also to have consistent wool from stem to stern. A consistent, contaminant-free (and hair is a dreaded contaminant in wool harvest!) wool clip reduces costly steps in the textile manufacturing process.
- Australian researchers developed an injection to cause finewool sheep to shed their fleece all at once, but so far that’s caused vastly more problems to sheep, woolgrowers and wool processors than it has solved. While it’s true that shearing is expensive and good shearers are increasingly hard to find, the process is both quicker and gentler on sheep than any other approach today. It takes a good shearer less than 5 minutes to shear a sheep, and most wool sheep are shorn once a year which makes for a very efficient harvest indeed, and the sheep trot off the shearing floor lighter and ready for summer heat.
Our relationship with wool from sheep versus other fibers has changed significantly in the last century. In 1945, the U.S. sheep industry was in its heyday with 56 million head on the landscape for meat and wool production. The demand for wool in the first half of the 20th century came from its use in military uniforms during World Wars I and II. But according to the USDA, in 2024 that number sat right around 3 million, a decrease of almost 95%. If that rate of loss was in a native species, it would qualify for consideration for listing as threatened or endangered – and it’s not a stretch to say that the U.S. finewool industry is threatened.
A major reason we have seen such a decrease in the use of wool has been the introduction of “lower maintenance,” petroleum-based textiles such as polyester, nylon and acrylic. These fabrics were developed and started entering the market between the 1930’s to 50’s. As they gained popularity, we unknowingly introduced and increased microplastics into almost everything we eat, drink and breathe.
The world has a huge plastics problem. According to The Plastic Soup Foundation, 33% of dust that is floating around your household comes from microplastics originating from textiles. This could be greatly reduced by replacing petroleum-based textiles with those made of wool and other grown fibers such as linen, hemp, cotton, ramie and silk. This would also help with the estimated 317,000 tons of raw wool that goes to waste each year that is referenced in the New York Times article.
The world has a huge plastics problem. This could be greatly reduced by replacing petroleum-based textiles with those made of wool and other grown fibers such as linen, hemp, cotton, ramie and silk.
Linda Poole
According to The Plastic Soup Foundation, 33% of dust that is floating around your household comes from microplastics originating from textiles.
While a lot of that “wasted” wool isn’t suited to clothing manufacture, there are myriad other uses for it. The NYT article noted that the Formafantasma – Oltre Terra” exhibit is exploring new ways to use excess wool for sustainable design and mentions working with Italian furniture company, Tacchini, “to manufacture sofas using surplus wool for the interiors, as a replacement for industrial foam.” Good on them, I say, because finding alternative uses for wool is essential to revive dying markets for this incredible fiber.
A lot of wool grown in the U.S. isn’t from finewool sheep, but that doesn’t mean it’s waste wool. What isn’t suitable for next-to-skin apparel can be useful for other textiles and products, from outerwear to upholstery to rugs and even obscure things like baseball innards, piano key felts and building insulation. That’s where the sofa manufacturing comes in. I wouldn’t call wool used this way to be waste wool, but instead would say it’s coarser wool serving important purposes other than luxury undergarments.
But there is true waste wool from every sheep sheared, which consists of short and dirty bits coming mostly from around the edges of the sheep, or parts of the fleece full of vegetative matter. Today there’s burgeoning interest in finding profitable, earth-friendly uses for this grade of wool. Some shepherds are using machines to press the dirty wool into small pellets that can replace fertilizer and peat moss in gardening soils. My fellow shepherd Becky Weed and I have been experimenting with several ways to use waste wool to combat water scarcity and improve soil health. It’s hard to beat compost made from wool, and felted wool products have great applicability for erosion control and water conservation.
So for those of us who love and steward the land, there’s much to admire about sheep. And when it comes to fiber, wool is the best for the West because you don’t need a tractor to grow or harvest it – wool is the most wildlife and water friendly of fibers and deserves more articles in the national press!
Sorry, the comment form is closed at this time.
Gary Andrews
Wow, what an informative article! Thank you for writing it.
Anna Jeane Anderson
Fantastic article!
Well researched and informative!
Please submit this to the NYT!
Evaline Woodrey
Wool comforts are excellent. I have 2 Wool comforts made from wool grown on a sheep I raised on a bottle. I am 90 years old and was 12 when I got the lamb to raise. I’m still using one of the comforts.